Automated cooler assembly line (VW)
Our automated workplace for the manufacture of a new type of cooler = increased productivity and quality of production
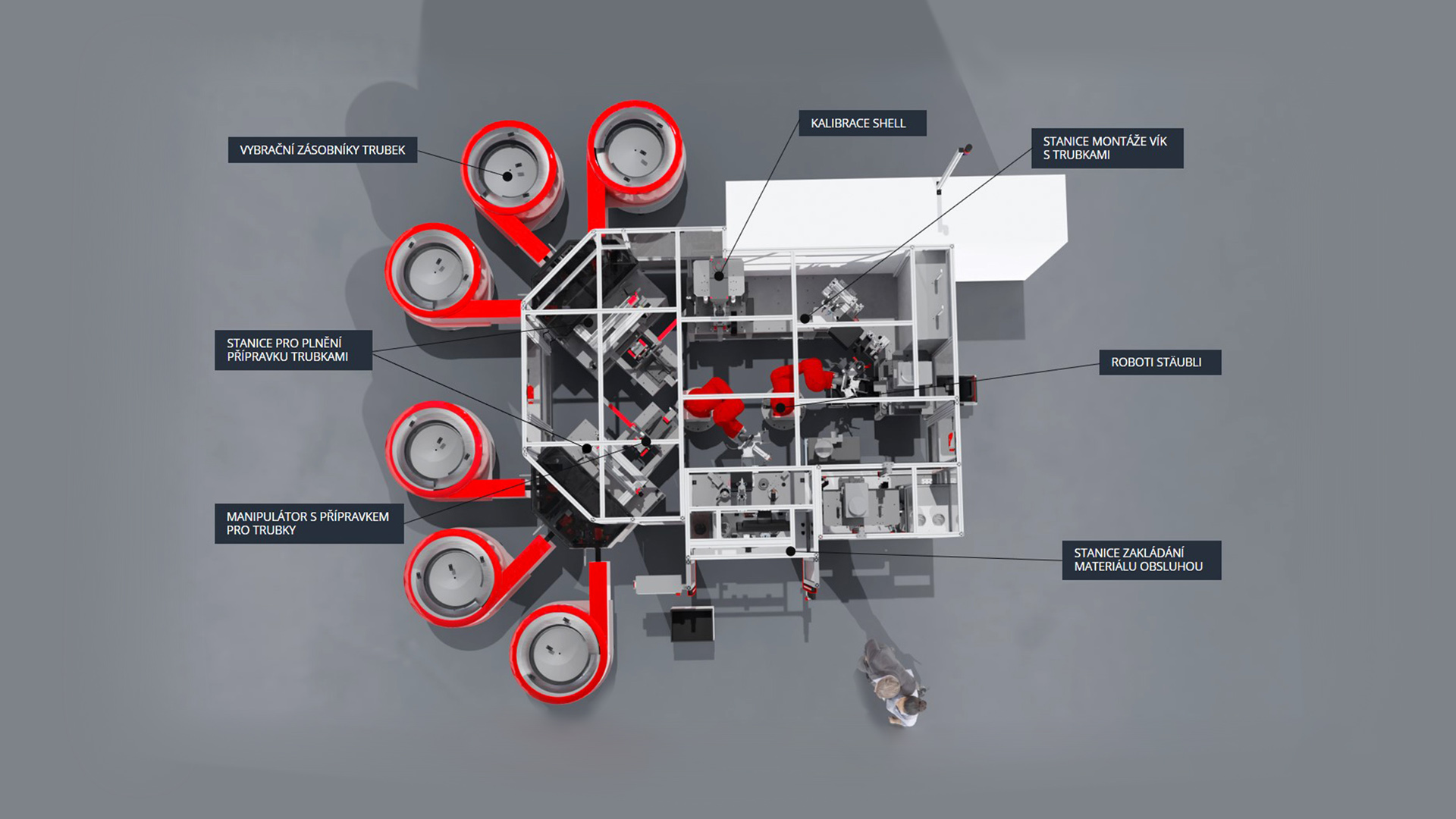
Basic parameters
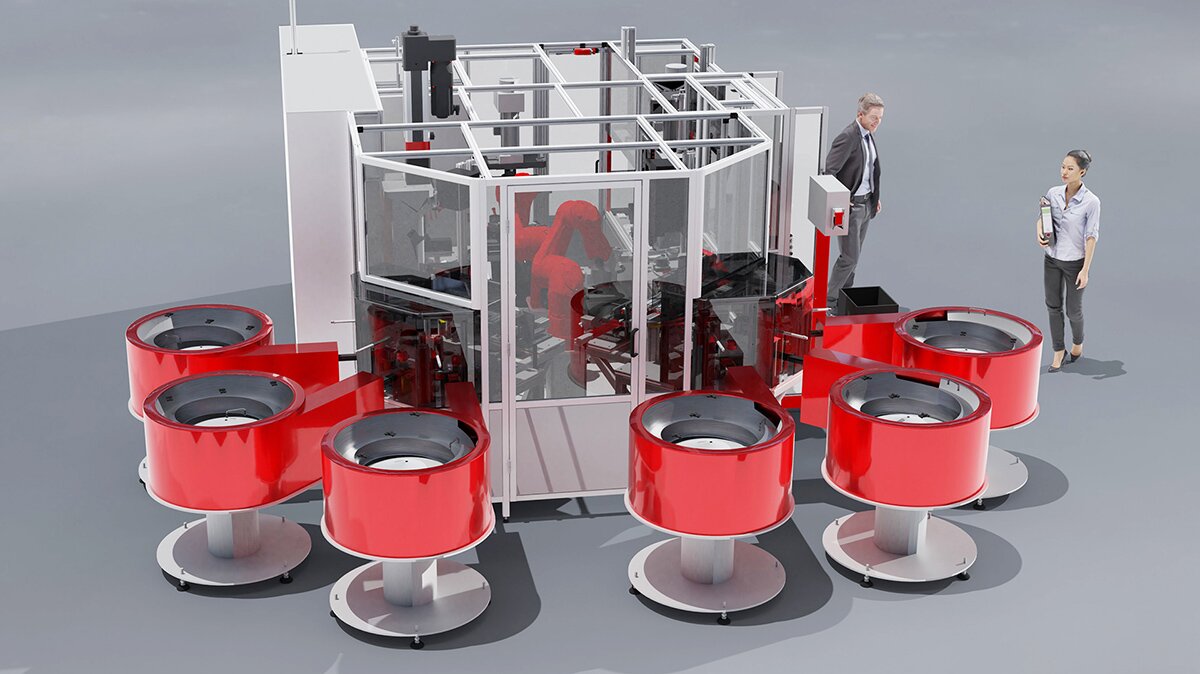
General view of the line
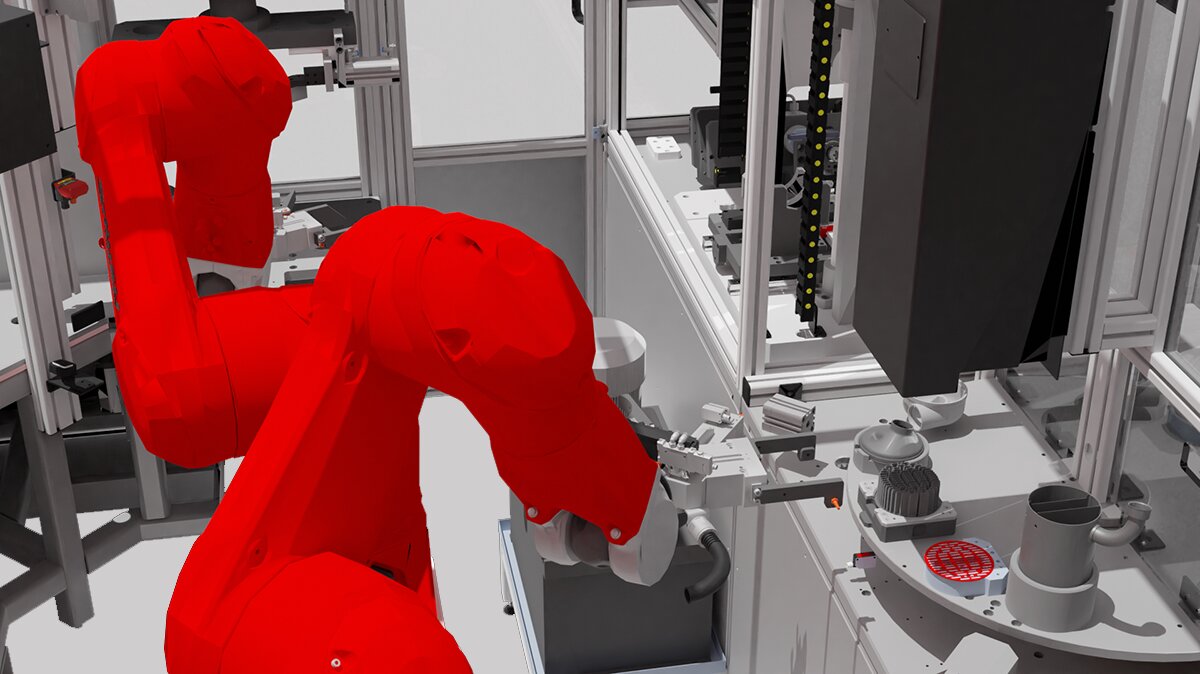
The robot is about to grab a part for assembly
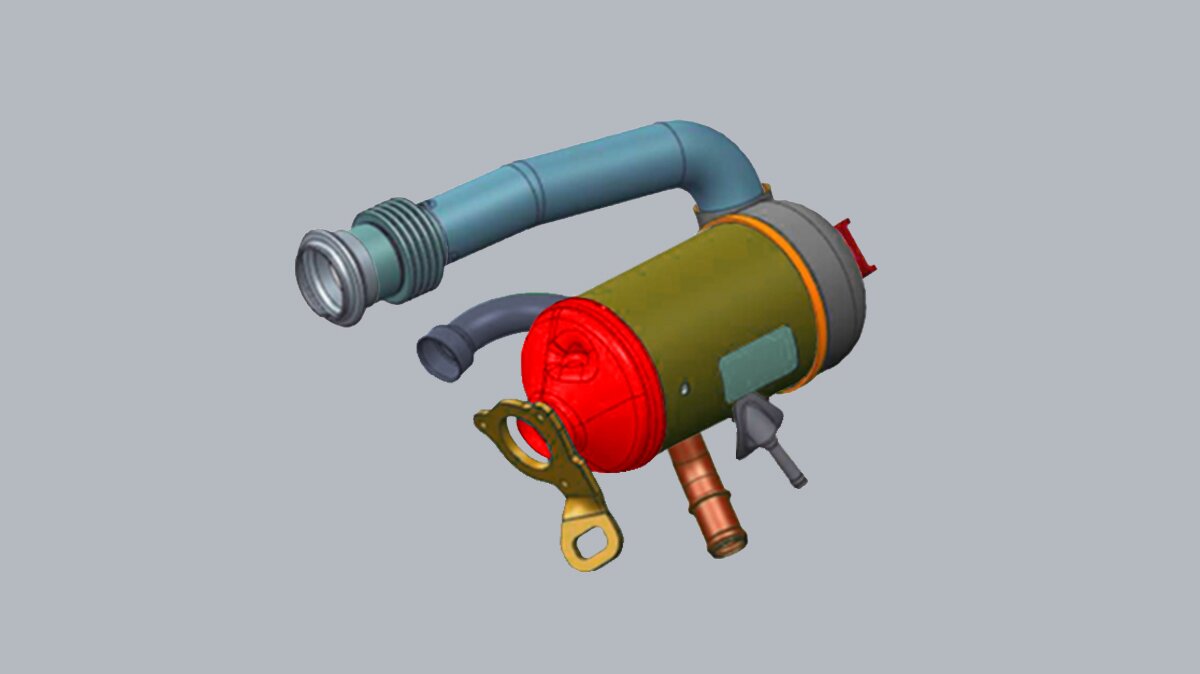
Radiator assembly
DELIVERY OF AN AUTOMATED WORKPLACE TO ASSEMBLE THE COOLER – USING ROBOTIZATION
Name of contract: Cooler assembly for the EGR module
Term of delivery: 2018–2019
SPECIFICATION:
The customer’s main requirement was focused on increasing the quality of production, saving on manpower and increasing productivity in manufacturing a new type of cooler. Our solution is based on the delivery of several automated workplaces operated by robots.
SOLUTION – PARAMETERS:
Line cycle: 1 unit/55 sec
Capacity: 456 units/shift
DESCRIPTION OF THE AUTOMATED PROCESS:
- Inserting individual components and removing the finished product by the operator.
- Insertion, orientation and handling of tubes.
- Calibration of the outer shell – shell and partitions.
- Pasting the inner partitions of shell tubes.
- Threading and sealing tubes through the lids.
- Installing the upper and lower flanges.
- Laser marking of DMC code.
BASIC CHARACTERISTICS:
- Vibrating feeders for input parts.
- Manipulators with jigs for working with tubes.
- The parts are handled by two Stäubli robots with grippers of our own design.
- TOX pressing equipment.
- Pasting and calibration equipment.
- Laser welding equipment.
- ROFIN laser marker.
- Camera check.
- The equipment is run by one operator.
Klíčové benefity našeho řešení:
- Minimizes scrap to around 0%
- Product assembled in shorter times
- Eliminates manual inputs into the product assembly process
- Manpower savings – the device is fully automatic
- Minimizes production cycle time
- Reduces the financial costs of ensuring the assembly of the cooler