Robotized depalletization and suspension of aluminum wheels
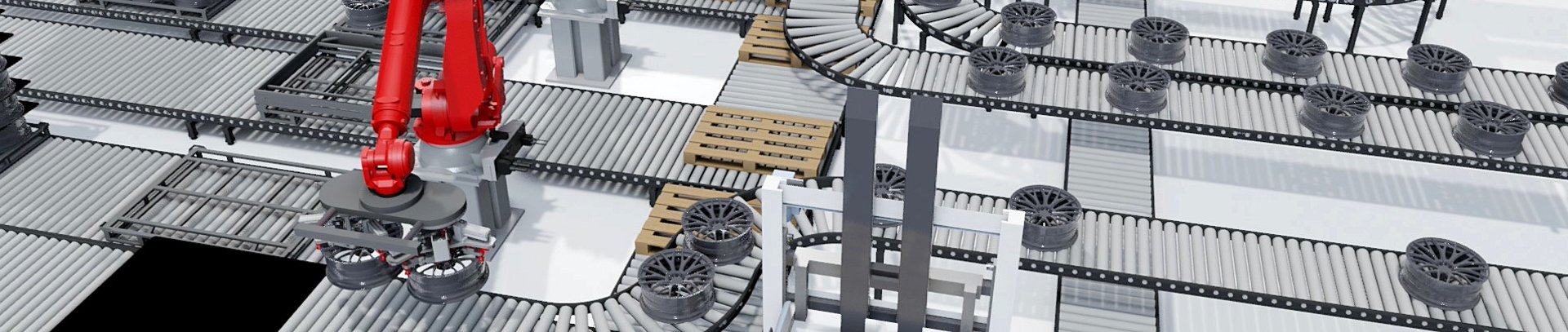
Dependable sorting
and suspension of aluminum wheels prior to painting
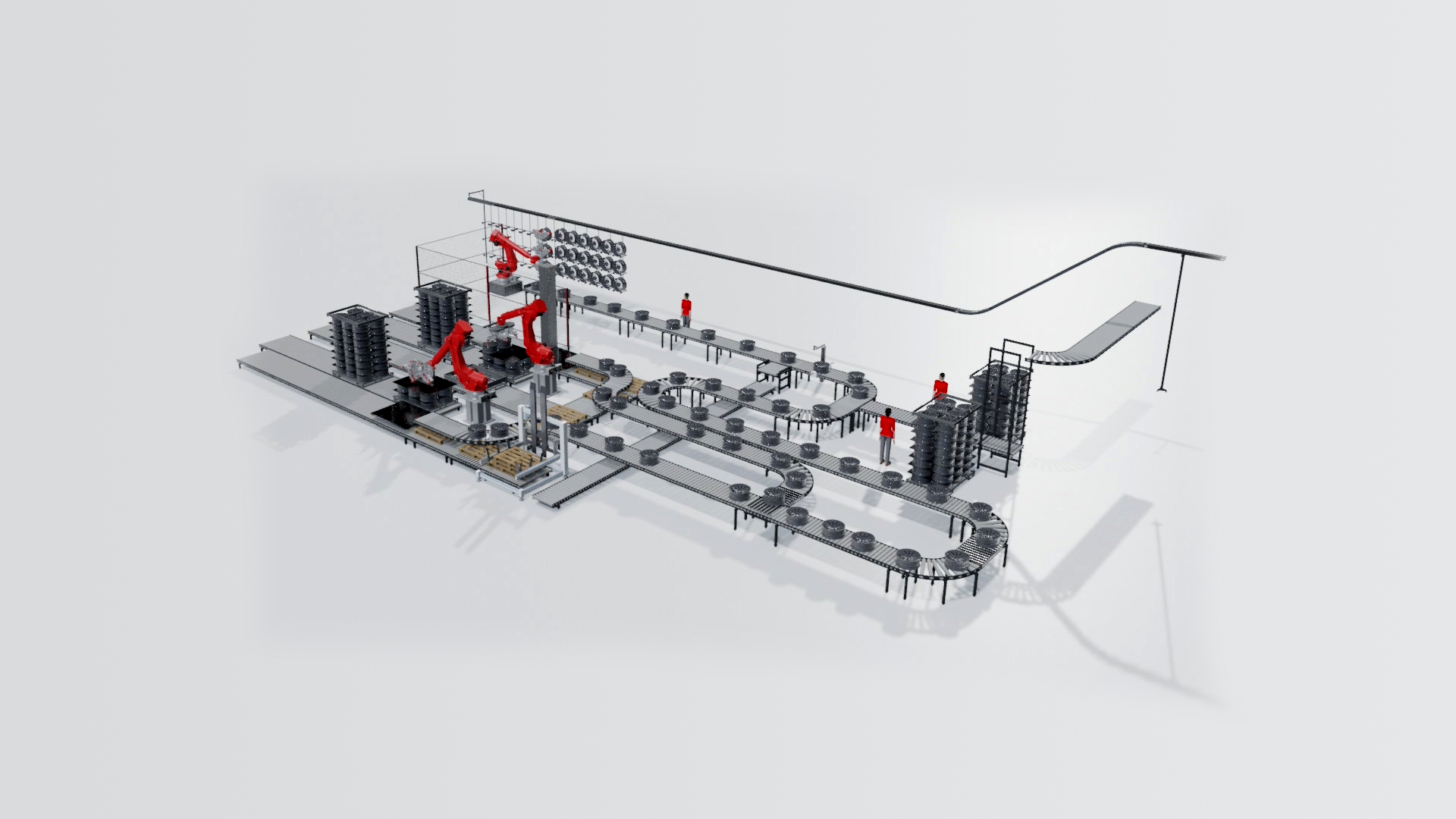
Basic parameters
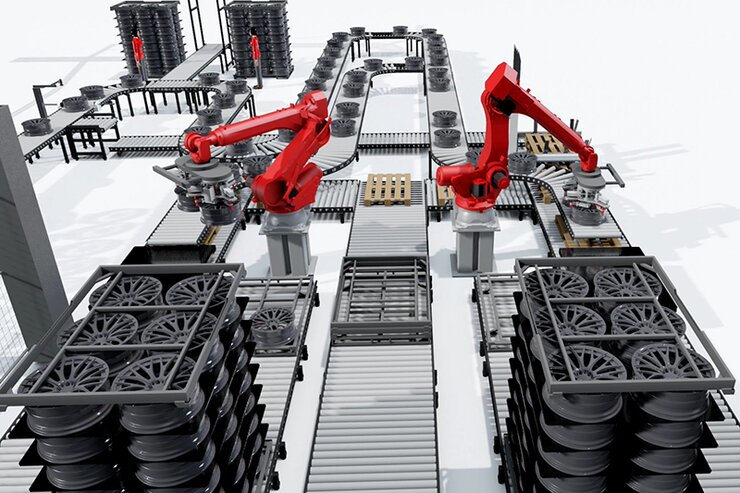
Initial depalletizing
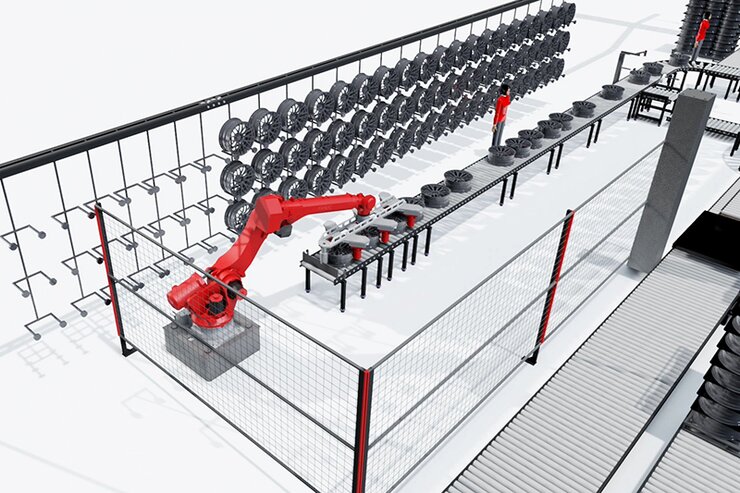
Gripping three wheels
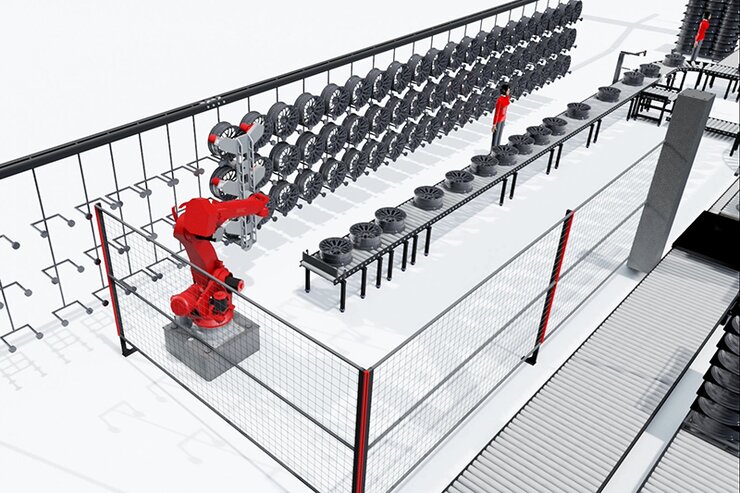
Relocation of wheels to the overhead conveyor system of the paint shop
Basic features
The concept includes a line for the robotic depalletizing of aluminum wheels from EWPS pallets, where the wheels are transported by a conveyor system to a robot that suspends them on the overhead conveyor system of the paint shop. In this way the suspended wheels are made ready for painting.
Description of the workplace:
1 – Conveyor system for transporting stored wheels for depalletizing, 2 – Conveyor system for transporting EWPS pallets, 3 – Robots designed for the depalletizing of aluminum wheels, the handling of mats and EWPS pallets, 4 – Conveyor system for transporting depalletizing wheels, 5 – Pallet tray, 6 – Camera system for checking the type of wheel before suspending, 7 – Conveyor system for wrong or unrecognized wheels, 8 – Pick-up centering point for the suspension robot, 9 – Suspension robot, 10 – Suspended conveyor system for the paint shop, 11 – Conveyor system for manual depalletizing, 12 – Conveyor system for WIP connection (automatic storage), 13 – Manual suspension workplace.
Description of the automated process
► The wheels from the pallets are removed from the conveyor system by two robots and are placed in a row on two separate conveyors, one after another.
► Plastic mats between the wheels and metal EWPS pallets at the top and bottom are sorted and placed on other separate conveyors.
► The depalletizing robots are coordinated with each other, so in case of the failure of one robot, the other one is able to work independently.
► Both conveyors with wheels then converge into one conveyor, while wheels from the automatic warehouse can also be connected to this conveyor.
► The camera system for checking the type, design and size of the wheel detects incorrect pieces – these pieces are then sent separately to the NOK conveyor.
► At the end of the conveyor, the suspension robot removes the wheels in threes and places them on the overhead conveyor system of the paint shop. To do this, it uses a special gripper for handling three wheels. The suspension robot works independently of automatic depalletization.
► In the event of the failure of any robot, the workplaces are prepared to work manually with the wheels, whether the manual depalletizing or suspension of the wheels.
► All automated handling of the wheels is done without damaging them and the manual handling workplace contains protective elements against damaging the wheels.