Machine 3 – the roller subassy completion and pressing of the pinion
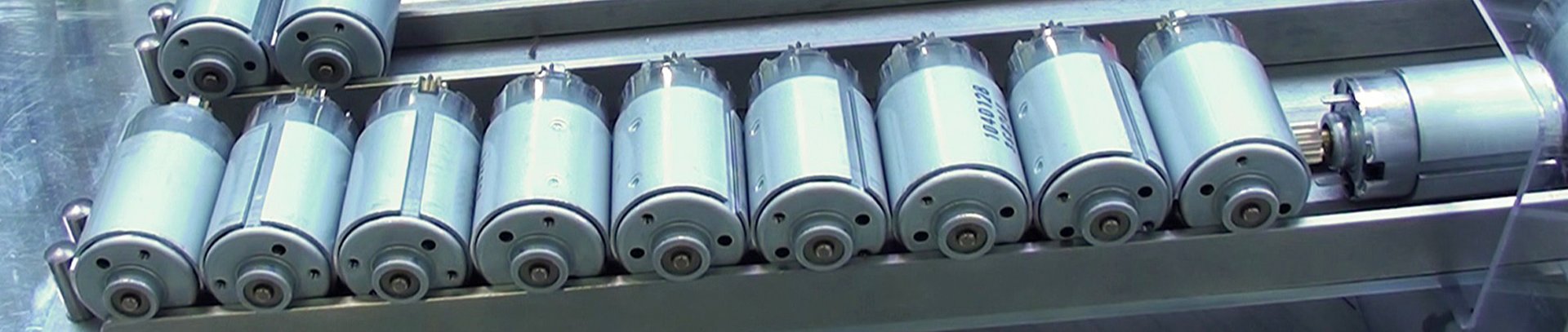
No. 3 machine of semi-automated production line for assembly of 3rd generation Audi EGR valve with subsequent adaptation for the alternative assembly of the 2nd generation EGR valve.

Machine with two workstations for the roller + roller bush automatic assembly and semi-automatic pressing of the pinion onto the DC motor
Project: Assembly line for EGR valve - Audi V6
Number of workstations within the plant: 2
Implementation date: 2015 - 2016
PARAMETERS:
Width: 1800 mm
Depth: 1650 mm
Height: 2000 mm
Operating pressure: 0.6 MPa
FEATURES:
The machine is one of the first assembly devices in the process of EGR valve completion.
The machine´s job at the first workstation is the automatic assembly of the roller + roller bush subassy, which is part of the valve shaft subassembly.
At the second workstation, the machine presses pinion onto the shaft of the DC motor.
(1) ROLLER (1) DC – MOTOR
(2) ROLLER BUSH (2) PINION
WORKPLACES´ EQUIPMENT:
The equipment requires a one-person operation and contains two independent workstations, one fully automated and the other semi-automated.
DT1 workstation
DT1 is a fully automated workstation for pressing the roller and roller bush. Vibrating feeders replenish the individual components, elements are then automatically inserted into the fixing jigs, and after the camera check, the parts are pressed. Assembled OK parts are going through the output chute to the next machine, or a box located in the lower part of the station.
DT2 workstation
DT2 is a semi-automated workstation where the pinion is pressed onto the DC-motor. The operator adds pinions and DC motors to the hoppers. The automated workstation places the DC motor and pinion in the fixing jigs, checks for the component´s presence and correct position, and presses the pinion onto the DC-motor shaft.
PINION and DC-motor The final assembly
DESIGN OF THE MACHINE:
- The lower part is made of 60×60×6 steel beams, in the upper part ITEM beams
- Solid/polycarbonate panels – as fixed surfaces or as doors,
- Workplaces protected with electric security locks or bolted connections
- Electrical switchboard with integrated operator panels and controls at the rear of the machine,
- OK and NOK boxes at the bottom of the apparatus together with an air purifier.