Machine No. 4 for automatic stem assembly
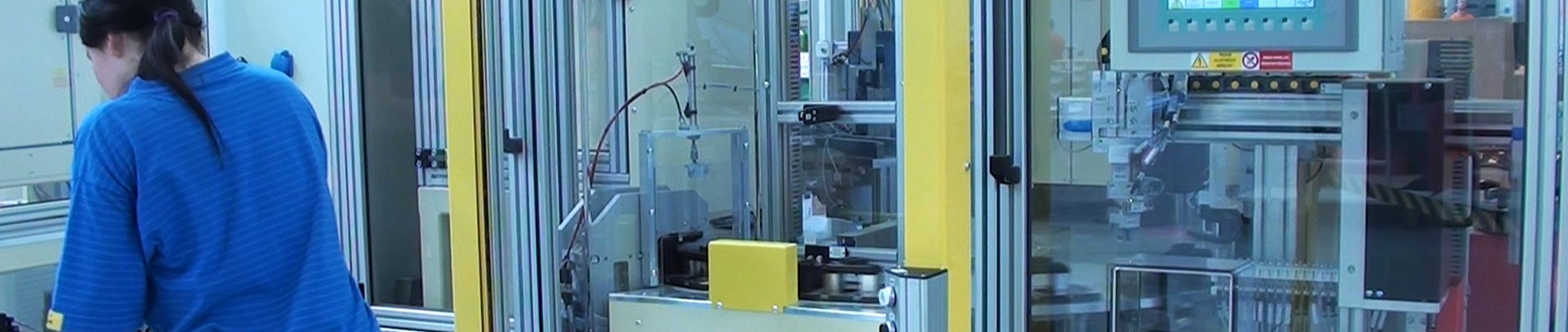
No. 4 machine of semi-automated production line for assembly of 3rd generation Audi EGR valve with subsequent adaptation for the alternative assembly of the 2nd generation EGR valve.
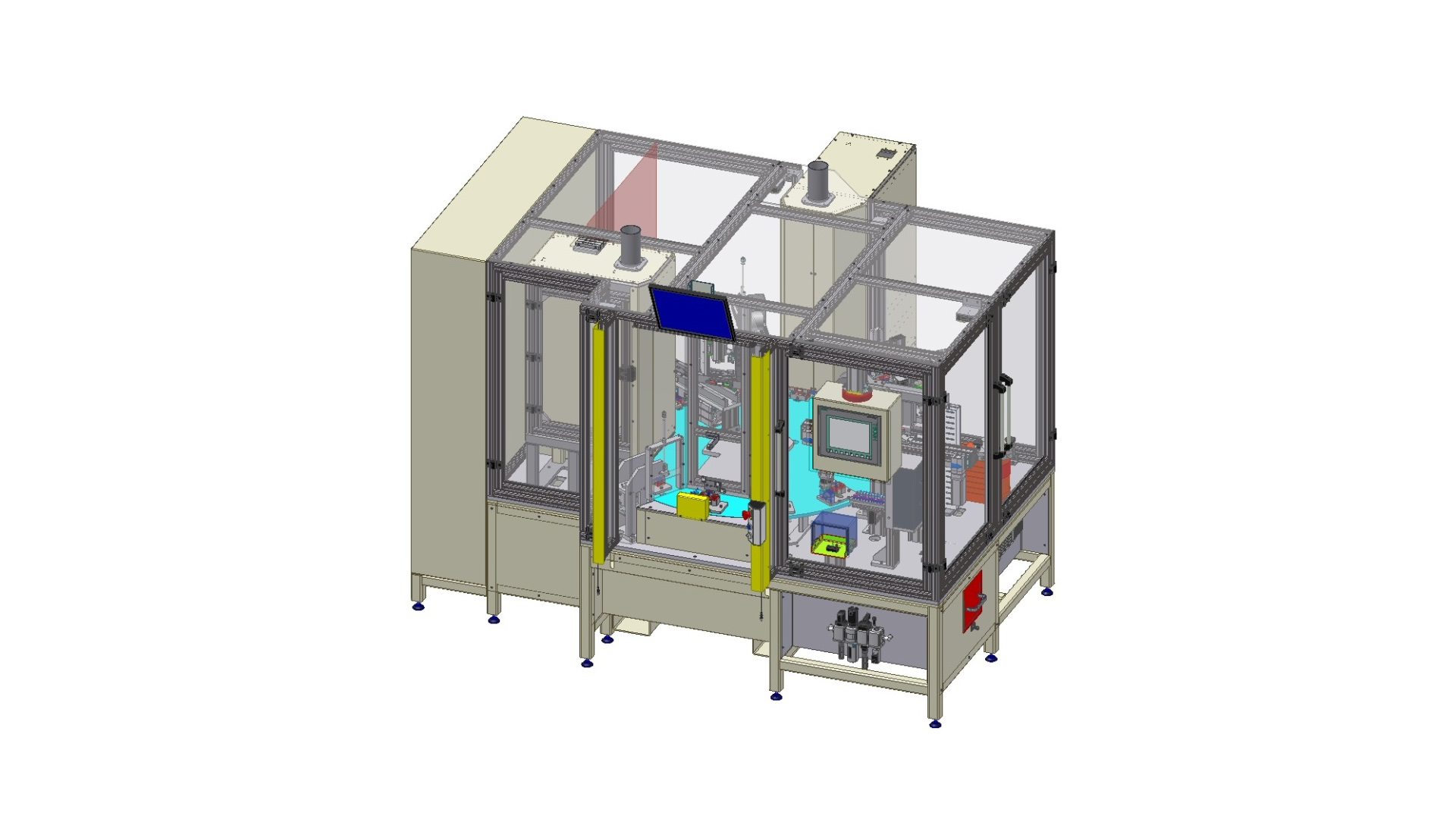
Machine for the automatic production of the EGR valve stem assembly
Project: Assembly line for the EGR valve – Audi V6
Number of workstations within the machine: 12
Term of delivery: 2015 – 2016
PARAMETERS:
Width: 2900 mm
Depth: 2290 mm
Height: 2000 mm
Weight: 2250 kg
Operating pressure: 0.6 MPa
FEATURES:
The entire equipment is construed as a single working unit with 12 workstations for a single operator. Over several steps the equipment assembles 4 parts into the final form of the stem assembly.
WORKPLACES´ EQUIPMENT:
The machine is designed as a twelve-position turntable. In the first position, the operator loads the input material into the machine and removes the finished OK pieces. The remaining 11 positions are performed by the automated stem assembly unit.
The following parts are used for assembling the valve stem:
Look at the deployment of individual workstations
Workstation 1 – Inserting parts and removing OK pieces
Workstation 2 – Installation of the STEM into ROLLER SUPPORT
Workstation 3 – Welding the STEM – ROLLER SUPPORT
Workstation 4 – Camera inspection of the welded STEM– ROLLER SUPPORT
Workstation 5 – Installation of the ROLLER AXLE into ROLLER SUPPORT
Workstation 6 – Rotation before welding
Workstation 7 – Welding the ROLLER AXLE – ROLLER SUPPORT
Workstation 8 – Camera inspection of the welded ROLLER AXLE – ROLLER SUPPORT
Workstation 9 – Gluing and inserting the magnet
Workstation 10 – Crimping the magnet
Workstation 11 – Glue curing + crimping check
Workstation 12 – Checking the position of the STEM nest
DESIGN OF THE MACHINE:
- Robust steel frame with closed rails for ease of handling with a forklift,
- Solid/polycarbonate panels – as fixed surfaces or as doors
- Workspaces are secured with optical security barriers, electric security locks, or bolted connections
- Operator panel, a panel with control buttons and monitor for displaying the results of weld inspection and crimping directly at the operator’s station
- Electrical switchboard located to the left of the machine operator’s station