Machine No.9 – tightness and operation test (Leaktester)
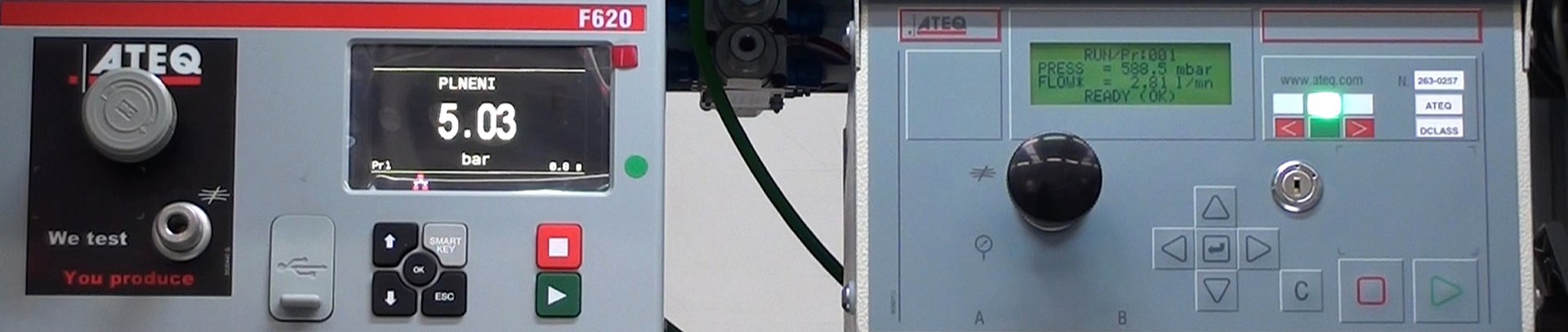
No. 9 machine of semi-automated production line for assembly of 3rd generation Audi EGR valve with subsequent adaptation for the alternative assembly of the 2nd generation EGR valve.
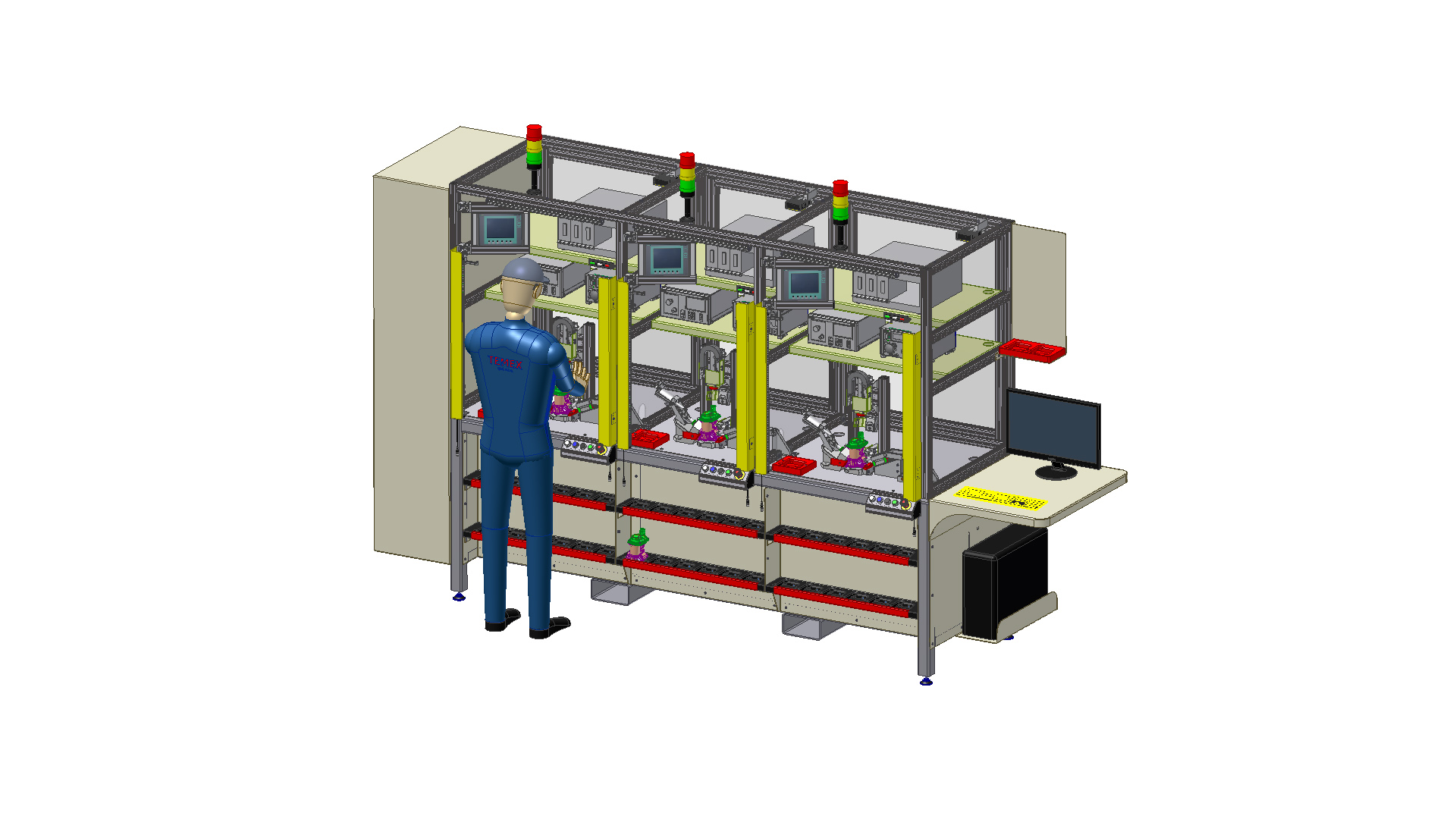
Machine for tightness and operation testing of the EGR valve (Leaktester)
Project: Assembly line for the EGR valve – Audi V6
Number of workstations within the machine: 3
Term of delivery: 2015 – 2016
PARAMETERS:
Width: 2000 mm
Depth: 800 mm
Height: 2000 mm
Weight: 900 kg
Operating pressure: 0.6 MPa
FEATURES:
The machine provides valve functionality testing and valve leakage testing. Testing takes place at three equal workplaces, which are operated by one operator.
DESCRIPTION OF THE WORKSTATIONS:
DT1-DT3 workstations
Each of the testing workstations performs these essential functions:
• Inserting and scanning a specific valve
• Valve chip programming
• Checking the tightness of the valve housing through the V-SEAL insert, test pressure 5 bar
• Checking the tightness under the poppet, test pressure 600 mbar
• Checking the operation of the lifting mechanism
• Valve chip lock
• Color in-jet marking of a good piece
Inserting and removing the tested EGR valve is done manually, starting the process with buttons, signaling with indicator lights, beacons, and on the OP. The machine can evaluate the number of scrap pieces for the relevant (optional) time period, including separating them according to the type of defect and date of manufacture.
DESIGN OF THE MACHINE:
- The lower part is made of 60x60x6 steel beams, in the upper part ITEM beams
- Solid/polycarbonate panels – as fixed surfaces or as doors
- Workspaces are secured with optical security barriers, electric security locks, or bolted connections
- Each workstation equipped with an operator panel in an adjustable angle design
- Each workstation equipped with shelves for keeping measuring instruments
- All workstations equipped with control buttons and shelves for nonconforming products
- Electrical switchboard located on the left side of the machine
- Terminals, aerators, air treatment unit, and paint pressure tanks located in the bottom part